gongjigongyi.com
与米乐m6网页版登录入口代表实时聊天。 工作时间:上午 9:00 - 下午 5:00(太平洋标准时间)。
致电我们
工作时间:上午9:00-下午5:00(太平洋标准时间)
下载
下载手册、产品技术资料、软件等:
反馈
New Tektronix battery simulator helps Nowi to supercharge the world’s drive towards autonomous energy
Learn more about the products mentioned in this story here:
- Keithley 2281S-20-6 Precision DC Supply and Battery Simulator
- Keithley 2450 Source Measurement Unit (SMU)
- Keithley DMM6500 Multimeters
Energy harvesting has huge potential for minimising energy loss and dramatically cutting the number of batteries that have to be discarded. To get the best results, Nowi must test its energy harvesting chips against a vast range of battery types.
The world is moving towards a digital future, including greater implementation of technology based around the Internet of Things (IoT) with its billions of connected devices. However, this comes at a price because these sensor-based systems rely heavily on the use of batteries. E-waste has the potential to become a significant problem, with around 15 billion primary batteries currently being disposed of every year, a figure that is set to increase as more wireless sensors are installed around the world. Fortunately, there are companies like Nowi, a semiconductor company based in Delft, Netherlands, that are striving to create ground-breaking solutions to combat this, with the help of Tektronix equipment.
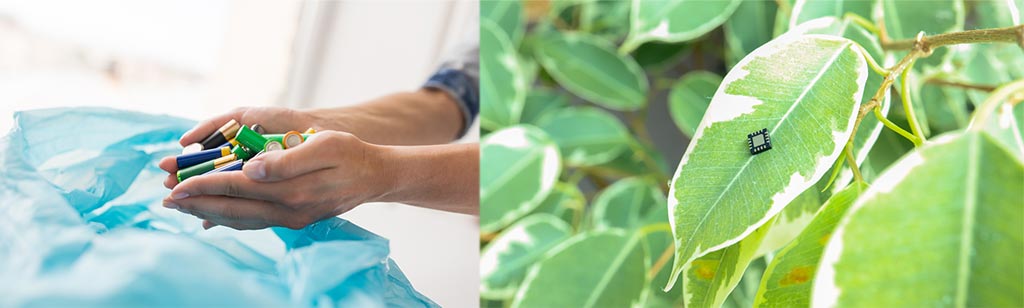
Harvesting energy to create autonomous power sources
Nowi specialises in the development of energy harvesting power management technology. Winner of nine innovation awards, the company identified that power supplies represented a critical bottleneck for IoT systems, with low-power devices requiring a cable or battery, options that are too expensive or impossible to implement for many IoT set-ups. It is simply impractical, for example, to keep changing batteries in sensors that are built into bridges or roads.
The IoT sector – and others – needed an environment-friendly solution that made it possible to develop energy autonomous products that would eliminate the need to swap or replace batteries. Energy harvesting is the answer because it enables ambient energy generated by light movement or vibration to be captured and used to provide an autonomous power source. Nowi believes that energy harvesting can help to ensure a sustainable future for electronics by reducing the sector’s global footprint. Not only does energy harvesting help the planet by reducing the number of batteries being discarded but it also cuts down the amount of raw materials that need to be mined to create long-life batteries.
The Nowi team has developed energy harvesting PMICs (power management integrated circuit) for low-power IoT devices which are small, simple to use and deliver high performance levels. Nowi PMICs significantly reduce the bill of materials (BoM) and have a PCB assembly footprint that is 30 times smaller than the competition. At the same time, the chip is capable of continuously adapting to its environment, maximising the amount of energy that’s harvested.
The challenge of characteristics
Nowi’s energy harvesting chips are the interface between a harvester such as a solar cell and a re-chargeable battery. The company needed to have the capability of carrying out rapid tests under different battery conditions for a range of industry sectors and end uses, checking its chips against a wide variety of batteries in its testing laboratories.
Gerrit de Wagt, Nowi’s Senior Validation Engineer and Application Engineering Manager, commented: “In order to match the harvester, IC and battery precisely we need to know the characteristics of each battery. How does it operate, how much leakage is there, what’s the voltage stability, when do you need to stop charging or discharging – all that data is essential.”
However, waiting for a battery to charge or discharge to a certain state to get this data can take up to a day, which is not practical. The Nowi team concluded that to streamline its test set-up and boost its efficiency, it would need to substitute actual batteries with a battery simulator.
Collaboration with the right partner to combat challenges encountered
It was an easy decision for the Nowi team to choose the Keithley 2281S-20-6 precision DC supply and battery simulator from Tektronix. The team were familiar with the brand and its reliable name, and therefore chose to move forward with Keithley’s stable, low-noise 120W precision power supply. This simulator can reproduce different battery characteristics, or models, which have been previously created using a Keithley 2450 Source Measurement unit (SMU). The 2450 model is a 200V, 1A, 20W SMU which measures voltage, current and resistance while cycling (charging and discharging) batteries in a controlled way. This equipment was supplemented with four Keithley DMM6500 multimeters to monitor other voltages and currents around the circuit.
Gerrit said: “With currents so low it can take a long time to charge or discharge a battery but by being able to substitute a real battery with a simulator, we can easily jump to an almost empty battery state or a full battery state or simulate a different type of battery and compare them against each other. When a battery is almost empty, it has different characteristics towards the PMIC and the application and we now have a rapid way of evalsuating those. The simulator gives us a competitive advantage, especially when we interface with supercapacitors and hybrid supercapacitors and the SMU pairs up perfectly by creating battery models and recording their parameters with a script that can be replayed in the simulator.”
He added: “You need to mimic the use case as far as possible and the simulator allows you to do this using automation. Not only is it much easier and faster to compare batteries by swapping the different types but the simulator allows you to do more and to test a wider variety of batteries and applications. It’s great that we can now carry out all our testing with this fully integrated Tektronix-Keithley ecosystem incorporating power supply, battery simulator, SMU and DMMs, all managed by the KickStart application software that controls the full bench and provides rapid access to measurement data.”
Gerrit, like the rest of the team, believes that Nowi’s drive towards autonomous energy is going to have “a tremendous impact” on the environment by reducing substantially the number of batteries that would normally be discarded. He says a major part of this drive is down to the company’s solid relationship with Tektronix which gives it access to the very latest testing and measuring equipment.