As more and more electronic devices are powered by batteries, designing and testing the power management unit (PMU) or power management IC (PMIC) are very important steps in the product development process. The PMU/PMIC is the module in an electronic device that manages the battery.Testing a PMU/PMIC is essential to ensure that the product works correctly when the battery is in different states of charge, various amp-hour capacity levels, and at different battery impedances. The PMU/PMIC must also be tested to ensure that its charge/discharge function works properly and won’t damage the battery by over-charging or overdischarging.
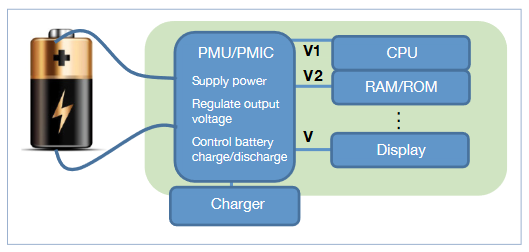
Traditional Test Method 1: Using a Real Battery
Traditionally, testing how the device under test (DUT) operates when the battery is in different states required connecting the DUT to a real battery. The test is conducted under the assumption that the open-circuit voltage (Voc) of the battery exactly corresponds to the battery capacity in a linear relationship. For example, if the Voc changes by 0.1%, the capacity will change by 0.1% or a constant factor x 0.1%. However, this is not the case with real batteries and can result in serious errors, since batteries from different manufacturers, or even from different batches from the same manufacturer, perform differently. In addition, it can take hours to charge or discharge a real battery, and the result can still be very inaccurate. For example, to measure a real battery’s charge cutoff voltage requires connecting the battery to a charger and then waiting a few hours for the battery to be fully charged.
Traditional Test Method 2: Using a Normal Power Supply
A general power supply can also be used for the test but will result in the following deficiencies:
- A general power supply cannot simulate battery resistance.
- A general power supply cannot respond to current changes quickly enough, which can cause unstable output voltage resulting in possible DUT damage.
Simulating a Battery Dynamically with the Keithley 2281S
Although many battery simulators have been introduced to address these problems, most are only capable of simulating the battery at a fixed condition, rather than dynamically.
However, the Keithley 2281S Battery Simulator can generate a battery model based on a real battery or import a battery model based on real data. The battery model can be saved as a .CSV file as represented in Table 1.
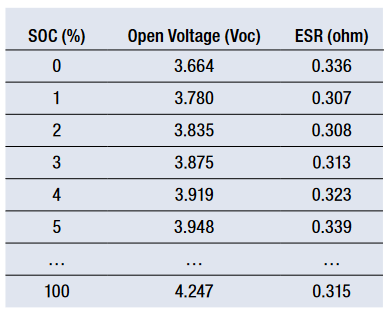
In addition, the battery model can be edited on a computer and easily imported to the 2281S. In the battery test function, choose MENU -> View -> Model, then select the model to import from a USB drive, as shown in Figure 2.

The 2281S can simulate a battery in real time based on the battery model. In Table 1, state of charge (SOC) represents the capacity in percentage, where 100% indicates that the battery is full, and 0% indicates that the battery is empty. Voc represents the open-circuit voltage of the battery, and ESR represents the battery resistance. The fine battery model contains 101 data points covering SOC from 0% to 100%, and a coarse model with 11 points is also available.
During battery simulation, the 2281S displays the Voc and resistance of the battery in real time, as shown in Figure 3.
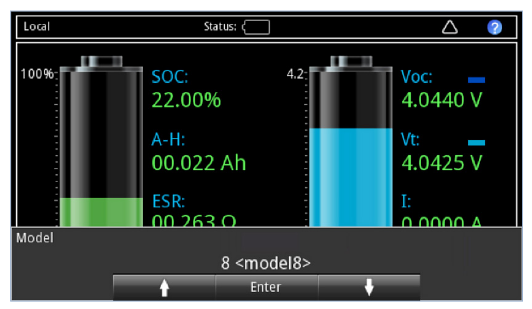
The battery can be set to any SOC or Voc state before the test. For example, Figure 4 shows the battery SOC is set to 22%, and the values of Voc and ESR change to their corresponding values at the SOC setting. Voc can also be set to any value within its range before the test.
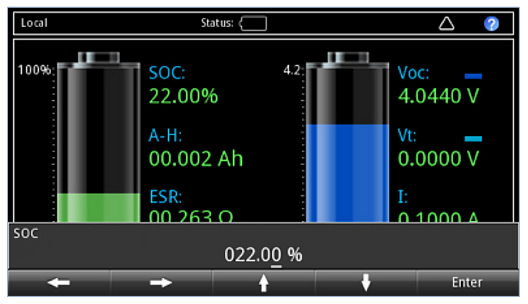
To reduce test time, battery capacity can be decreased to lessen the charging/discharging time. For example, with an initial SOC of 22% and real battery capacity of 2000 mAh, it can take hours to conduct a test to determine the point at which a battery-powered cell phones will turn off. However, when the battery capacity is set to 100 mAh, it takes only a few minutes for a cell phones or another DUT to turn off so that the battery SOC and Voc can be measured.
As shown in the top screenshot of Figure 5, set the battery capacity to 100 mAh. In this example, the PMU chip would turn a cell phones off when the SOC falls to 11.75% and the Voc falls to 3.9945 V, as shown in the bottom screenshot.
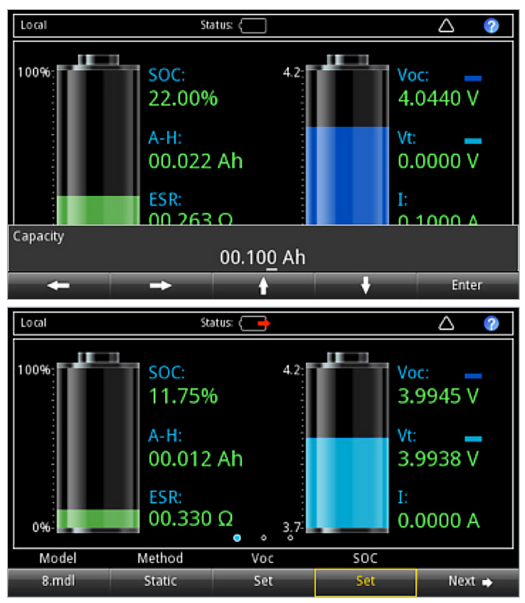
In addition, the 2281S battery simulator can absorb current up to 1 A, so testing of the PMU/PMIC during a battery charge cycle can also be performed. In addition, the battery SOC and Voc can be measured when the DUT's PMU stops the charge cycle.
Furthermore, the 2281S battery simulator supports two modes of simulation: dynamic and static. The mode can be changed by selecting Method in the soft key area of the home screen, as shown in the Figure 6. In static mode, a test can be performed at a fixed point of SOC and Voc.
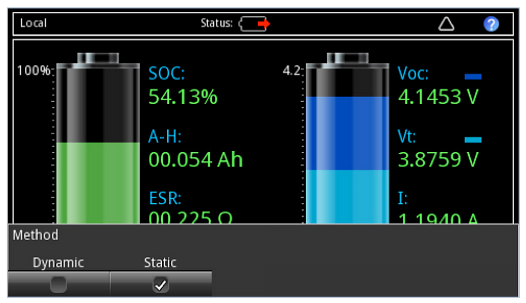
In the right part of the home screen, the real terminal voltage (Vt) of the battery is represented by light blue, and Voc is represented by a darker blue. The relationship of the two values is shown in the equation Vt = Voc – R * I where R represents the battery resistance (ESR) and I represents the charging/discharging current. The value of I is positive during discharging and negative during charging. Therefore, the value of Vt changes with load current changes.
If the 2281S is connected to the DUT with a four-wire, remote sensing connection, then the remote sensing compensates for the voltage drop due to the test lead resistance. However, if the 2281S is connected to the DUT with a two-wire connection, the voltage drop due to test lead resistance will result in a voltage at the DUT that is different than the voltage at the 2281S output terminals, Vt. In this case, a resistance offset can be set by choosing MENU -> Battery -> Setting. For example, Figure 7 shows the resistance offset set to -20 mΩ to cancel the test lead resistance.
Conclusion
The Keithley 2281S Battery Simulator and Precision DC Power Supply enables users to:
- Set up a customized battery model and import it to the 2281S to simulate a real battery;
- Set the battery state of SOC, Voc, and ESR at any value within their range before the test according to test requirements;
- Modify the SOC, Voc, test mode, and I-limit during the test;
- Decrease the battery capacity to increase test efficiency
In addition, battery tests can be performed with the 2281S to measure capacity and resistance and to generate a battery model.
With a battery simulator such as the 2281S, a PMU/PMIC can be fully tested efficiently and quickly.